1、A Graphite Electrode Used to Apply Pulse Current to Continuous Casting Tundish
Improving the strength, toughness, ductility, processing performance and service life of steel is one of the important research topics of the steel industry in the 21st century.
It is an effective method to change the metallographic structure and refine the grain size. It can be achieved by increasing the content of specific alloy elements in the steel, or by controlled rolling and controlled cooling and equal channel angular extrusion cold deformation technology. Electric pulse refinement of solidified metal structure is a new technology in the field of metal structure refinement.
The electric pulse refinement of the solidification structure of the continuous casting slab is mainly used to control the solidification structure of the continuous casting slab by applying a suitable pulse current to the molten metal before or during the solidification of the molten steel in the continuous casting production. This technology was first tested and studied in the field of non-ferrous metals, especially its influence on the solidification structure of Al, Al-5Cu alloy, Al-18% Si alloy, and Sn_15% Pb alloy.
In recent years, the technology has been introduced into steelmaking and continuous casting, such as the study of the effect of applying electrical pulses to the molten steel in the continuous casting mold or the tundish. The electrical pulse technology has a significant and stable refinement effect and has investment The advantages of less, simple equipment, flexible methods, and no pollution have attracted the close attention of many domestic and foreign researchers. Although the technology has made some progress in experimental research, the industrial application electrode still needs to meet the following two requirements: the installation method of the practical electrode needs to be improved; the electrode resistance to high temperature oxidation and corrosion needs to be improved, and it needs to be longer. The use performance of time, try to achieve the same life as the tundish lining. The conductivity of practical electrodes needs to be improved, and the resistance should be reduced as much as possible to increase the conductivity.
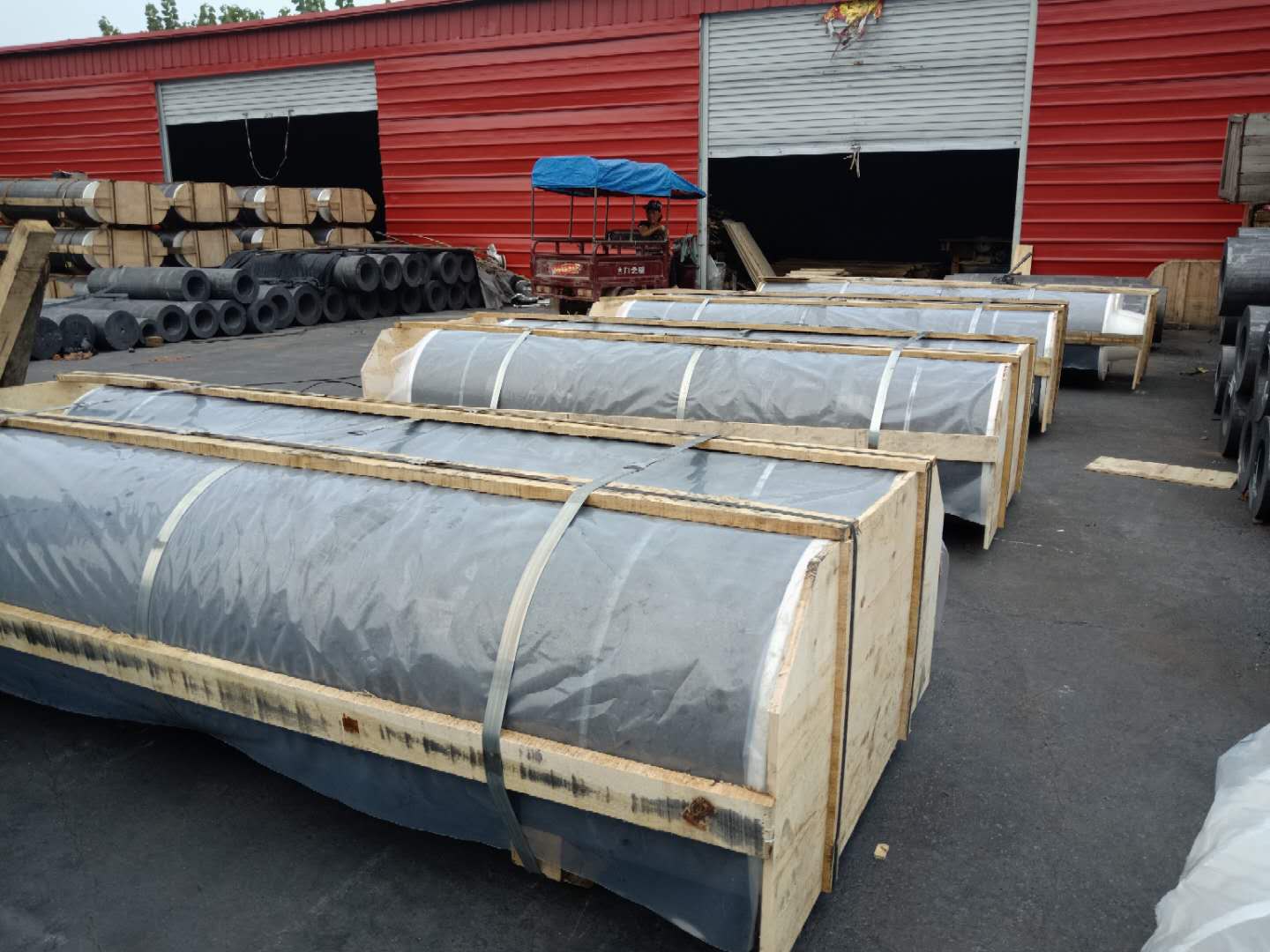
Graphite electrode steelmaking is to input electric energy into the electric arc steelmaking furnace through the graphite electrode, and the electric arc generated between the electrode end and the charge is used as the heat source for steelmaking. The electric arc furnace uses electric energy as the heat source, and the atmosphere in the furnace can be adjusted, which is extremely beneficial for smelting steel grades that contain more oxidizable elements.
When smelting various alloy steels and ferroalloys, graphite electrodes are used. At this time, a strong current is introduced into the smelting zone of the electric furnace through the electrodes to generate an electric arc, which converts electrical energy into heat, and the temperature rises to about 2000 degrees, thereby achieving smelting or reaction. Purpose.
In addition, in the electrolysis of metal magnesium, aluminum, and sodium, the anode of the electrolytic cell also uses graphite electrodes. The resistance furnace that produces emery also uses graphite electrodes as the conductive material of the furnace head.
The produced graphite electrodes of various specifications such as ordinary/high power/graphite electrodes uhp/impregnation have the characteristics of wear resistance, high temperature resistance, corrosion resistance, impact resistance, oxidation resistance, and easy conduction and heat conduction.